Ethylene production presents some of the most challenging operating conditions in the petrochemical industry, including extreme temperatures, highly corrosive atmospheres, and flammable media. High-performance butterfly valves are crucial for ensuring the safety and efficiency of these complex processes. This article examines the key applications and technical requirements for these valves in ethylene plants.
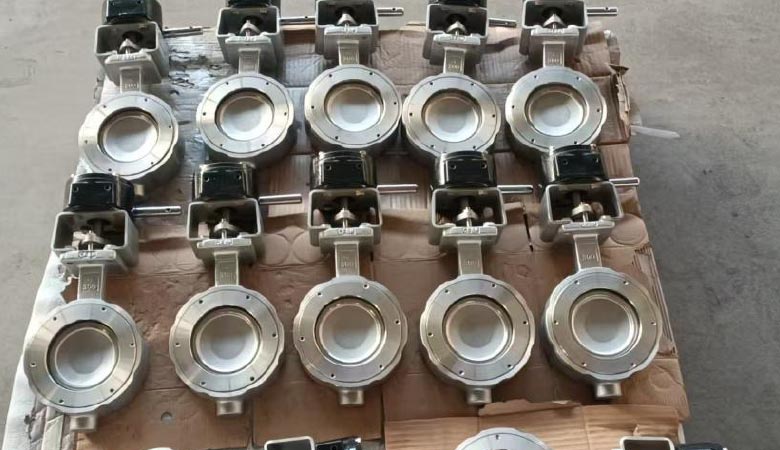
Key Applications in Ethylene Plants
- Cracking Furnaces and Quenching Systems:
- High-temperature cracked gas pipelines exiting cracking furnaces (800–1000°C, containing ethylene, propylene, H₂, H₂S).
- Regulation of high-temperature media in quenching oil/water systems (200–400°C).
- Cracked Gas Compression and Acid Gas Removal:
- Cracked gas compressor inlet and outlet pipelines (4–8 MPa, containing H₂S, CO₂).
- Control of NaOH circulating liquid in alkaline scrubbing towers.
- Deep Cold Separation and Ethylene Refrigeration Systems:
- Ethylene/propylene liquid phase pipelines in low-temperature separation towers (-100~-50°C).
- Refrigerant (propane, propylene) circulation systems.
- Ethylene Storage, Transportation, and Filling:
- Inlet and outlet pipelines for cryogenic ethylene storage tanks (-104°C).
- Control valves for ultra-low temperature liquid ethylene at filling stations.
- Flare Gas and Waste Gas Treatment:
- Flare gas header (containing methane, ethylene, and other flammable gases).
- Regulation valves for waste gas incineration systems.
- Steam and Thermal Systems:
- High-pressure steam pipelines for cracking furnaces (10–15 MPa, 400°C).
- Turbine-driven steam regulation valves.
Critical Technical Considerations
- Material Selection:
- High-temperature cracked gas: Inconel alloys + ceramic coatings.
- Cryogenic ethylene: 304L/9% nickel steel + low-temperature elastomer seals.
- Acidic media: Duplex steel/Hastelloy alloys + hard alloy seals.
- Sealing Design:
- High temperature and pressure: metal hard seals + elastic compensation rings.
- Cryogenic conditions: Multi-layer bellows seals + vacuum insulation structures.
- Safety Features:
- ATEX/IECEx certified pneumatic actuators.
- Fire safe design.
- Anti static designs.
Valve Selection and Maintenance Best Practices
- Selection:
- Match materials and sealing configurations to media properties and operating conditions.
- Ensure valves meet relevant industry standards (API, ASTM, ATEX/IECEx).
- Select appropriate actuators for precise control and safety.
- Maintenance:
- Regularly inspect sealing surfaces for coke buildup and perform online high-pressure steam cleaning.
- Nitrogen purge cryogenic valves during storage to prevent moisture and minimize assembly stress.
Advantages of High-Performance Butterfly Valves
- Extreme Temperature Resistance: Suitable for both high-temperature cracking and cryogenic separation.
- Corrosion Resistance: Materials designed to withstand harsh chemical environments.
- Explosion-Proof Safety: Certified designs to mitigate risks in flammable atmospheres.
- Efficient Flow Control: Enables precise regulation of process flows.
Conclusion
High-performance butterfly valves are vital for the safe and efficient operation of ethylene plants. By focusing on appropriate material selection, advanced sealing technologies, and rigorous maintenance practices, plant operators can ensure long-term reliability and minimize risks.
Contact Shengfei today for high-quality butterfly valve solutions tailored to ethylene plants processing needs.
Web: www.shengfeimachinery.com
Mail: sales@shengfeimachinery.com